The operational data of machines and plants often signals impending faults ahead of time. If this data is continually recorded and analyzed, errors can be corrected before they arise (predictive maintenance). But interpreting these data streams requires expert knowledge. A new approach by Siemens AI is making it possible to train artificial intelligence (AI) with this expert knowledge at minimal expense and effort.
Sebastian Mittelstädt – Head of Research Group in AI of Siemens Technology
Large industrial plants like those used in manufacturing, power generation, and power distribution require constant monitoring. In the past, this was exclusively done by engineers. But thanks to the IoT (Internet of Things), it has now become common practice for machines to be monitored primarily via sensors that record data like pressure, temperature, vibrations, etc. Changes in these values often indicate impending faults and wear much earlier than would be possible with traditional maintenance. “Detecting faults based on sensor data means analyzing endless data chains (or graphs) and finding anomalies,” explains Sebastian Mittelstädt, an artificial intelligence expert at the Siemens Technology Research Unit. “People generally find these tasks to be boring, subject to error, and laborious. On the other hand, artificial intelligence can easily be trained to perform these pattern recognition tasks. “We developed SALT (Semi-Automatic Labeling Tool) specifically for industrial applications. Using artificial intelligence, SALT helps analyze sensor data streams while getting better and better at it over time.”
On-the-job training instead of training data
All artificial intelligence has to be trained before it can be properly used. Most methods train AI using manually generated training data. But this generally requires thousands of datasets before reliable findings can be expected. “Reliable training data is costly and time-consuming to generate,” says Mittelstädt. “Experts have to prepare many thousands of datasets in such a way that artificial intelligence can learn from them. In the industrial environment, it’s always difficult to get real data on the system states and faults that are less common but are important for training.”
Expert in just a few hours
SALT uses a different approach. When it first starts training in real operation, “SALT can only detect areas where data patterns are significantly different and marks them with different colors. Usually, these aren’t faults but are simply different phases of normal operation. The human expert adds their own interpretation (label) to these colored areas – for example, temperature increase due to motor starting,” explains Mittelstädt. “Trained on the basis of this training data, AI is soon able to correctly identify the different phases of normal operation and assign them the right label. Whenever new and unfamiliar data patterns occur, AI marks them as anomalies that need to evaluated by the expert. Basically, AI and the expert work together like apprentice and master. The apprentice can soon carry out simple tasks independently and, whenever things get critical, calls in the master. We’ve already deployed SALT in various industries – for monitoring oil pumps, in the automotive industry, and in logistics and production. What we’ve found is that when artificial intelligence is trained by SALT and an expert, it’s already highly competent at interpreting data within just a few hours. In the case of traditional AI training using specially generated training data, it usually takes several days, if not months, before AI can be used.”
Labeled data – a perfect driver of industrial AI
“Access to high-quality, labeled data is essential for using artificial intelligence in industrial environments. We have to have this data to be able to train AI,” says Vladimir Lavrik, Senior AI Expert at Siemens Digital Industries (DI). For example, DI uses AI to prevent failures in a 3D printer. (see more) The printer has a nozzle that occasionally becomes blocked, and when it does, the part currently being printed is rendered unusable. The only way to keep this from happening is to detect the impending blockage based on data from the printer and clean the nozzle ahead of time. “SALT gives us reliably labeled data that can be used for training artificial intelligence to detect an impending blockage before it happens,” says Lavrik. “Efficiency is especially important, because if anything in the printing process changes – such as the material or temperature – the AI model has to be adapted using new training data.”
Vladimir Larvik – Senior AI Expert in industrial AI at Digital Industries
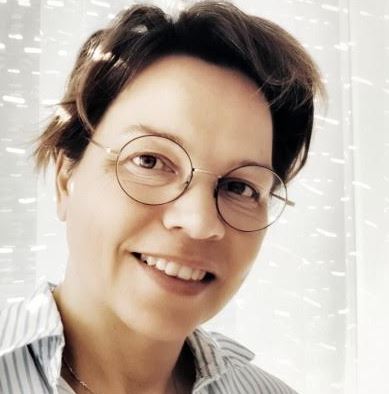