Cypress Semiconductor uses simulation to optimize touchscreen design for use in diverse products including smartphones, laptops, automotive and industrial applications,
home appliances, and more.
TO MAKE A PHONE CALL, compose a text message, or even to beat the next level of an Angry Birds game, we rely on being able to pick up our smartphone and interact with it without a second thought. No matter the size of our fingers, whether or not we have recently applied hand cream, or if the phone is resting on a flat surface, the touchscreen responds seamlessly, bringing just one more thieving farm animal to justice.
Engineers at Cypress Semiconductor, the leading supplier of smartphone touchscreen technologies and touch-sensing solutions, are hard at work mak¬ing this possible, ensuring that touchscreen applications perform flawlessly under a variety of conditions. “And it’s not just about smartphones,” says Peter Vavaroutsos, a member of the touchscreen modeling group at Cypress. “Our technologies are used in smartphones, mp3 devices, laptops, automotive environments, industrial applications, home appliances, and more. For each of these uses, a different design is needed.”
Capacitive touchscreens (see Figure 1, top) are by far the most commonly used method of touch sensing in the electronics industry, and consist of varying layers of transparent lenses, substrates, adhesives, and indium-tin-oxide (ITO) electrodes. Together, these elements are known as touchscreen panels (TSPs) or stack-ups. Depending on the type of product in which they will be used, each stack-up and electrode pattern is customized for its intended environment and use. A stack-up (see example shown in Figure 1, bottom) contains an LCD layer, followed by a sub-strate, a pattern of horizontally and vertically aligned diamond-shaped ITO electrodes, and finally an optically clear adhesive layer that bonds the glass cover onto the screen.
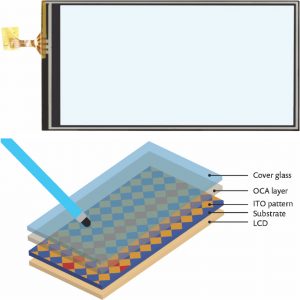
At Cypress, multiphysics simulation and simulation apps have emerged as key tools for ensuring effective product development, allowing designers to predict and optimize the behavior of numerous designs without needing to build multiple physical prototypes.
An Engineering Rule of Thumb
As a rule of thumb, touchscreens must track finger or stylus positions with high accuracy. This means that at any point in time, a touchscreen must not only be able to determine that it is being touched by an object of variable size, but also where, for how long, and whether the “touch object” is moving in a certain direction. To achieve this, a capacitive sensor is composed of a pattern of horizontally and vertically connected ITO electrodes, where a touch object is sensed at the grid intersection. When a finger or stylus touches the screen’s surface, it distorts the electrostatic field and causes a measurable change in the coupling capacitance between the transmitting and receiving electrodes (see Figure 1, bottom).
Depending on where and how the touchscreen will be used, the stack-up components are configured in a variety of ways. “The design of a touchscreen stack-up for the automotive industry is very different than one used in, say, a laptop,” says Vavaroutsos. “My job at Cypress is to design different stack-ups for different consumer products, taking into account such things as how interactions between a horizontally mounted GPS, for example, will differ from a smartphone, which can be held and interacted with in a myriad of different ways.”
Cypress R&D engineers create multiple electrostatic simulations for a particular device geometry and for many different parameters, what the team refers to as a “design box”.
“Our findings from a specific design box are then used by our sales engineers and customer support team so that they can optimize certain design specifications in order to meet a customer’s individual needs,” explains Vavaroutsos.
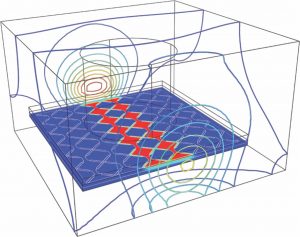
Using the COMSOL Multiphysics simulation software, R&D engineers at Cypress perform analyses to determine the electrical performance of the ITO pattern, including measuring the change in mutual capacitance between electrodes when a stylus or finger is present. In the example shown in Figure 2, floating potential boundary conditions were used in the electrostatic model, a feature that is instrumental in allowing Cypress engineers to simulate the boundaries of touch objects and any electric shielding or electrodes that are not currently being excited. Because these objects are affected by an externally applied electric field, they will be at a constant but unknown electric potential and therefore are represented as surfaces over which a charge can freely redistribute itself.
“Since the screen can be interacted with in so many different ways, in order to optimize a stack-up for use in a certain device or product, we have to run numerous electrostatic simulations in order to test different touch object positions,” says Vavaroutsos. “We try to minimize effects such as when you get water on your screen and it doesn’t work as well, or when you put your phone down on the table and the screen responds poorly. Simulation has been a very valuable tool for ensuring that our product responds effectively over a range of different environments and conditions, since we can single out certain factors and determine how to most effectively optimize performance. ”
Because COMSOL software can be run on unlimited multiple cores and using cluster and cloud computing with no limit to the number of compute nodes, Cypress engineers are able to quickly run many simulations with virtually no limits on the size of the design boxes analyzed. “We can reduce the number of assumptions we have to employ and accurately model capacitive touchscreens by capturing changes between active electrodes in great detail while working with realistic geometry and materials,” says Vavaroutsos.
Within a single design box, Cypress engineers might test different cover lens thicknesses, alter the permittivity of various layers, or change pattern parameters. Depending on the application area, a single touchscreen may be designed to have more than one electrode layer, or have different layers in a different order. For example, a design box might include a range for cover lens thicknesses from 0.5 millimeters to 1.5 millimeters. The R&D team at Cypress will model a variety of different parameter ranges in order to precisely understand a certain design, but anything outside the modeled range will remain unknown.
Touchscreen Simulation Apps for Customized Designs
In order to extend the usability of their models, Cypress engineers are using the Application Builder in COMSOL Multiphysics to create simulation apps based on their models. “In order to communicate more effectively with our customer support teams, we’ve started using the Application Builder to build simplified user interfaces over our models,” says Vavaroutsos.
“Before we started using simulation apps, any time a customer wanted a design that was slightly outside of the design box, we’d have to be involved again to run simulations for minor parameter changes. A lot of times, a sales engineer might try to run the simulations themselves, even though they had little experience using the COMSOL software. Not only would we have to check the simulations, but they also took up a seat on the software as well.”
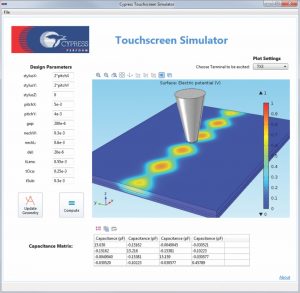
The example app in Figure 3 shows parameters that could be included in a touchscreen app. The finger or stylus touching the panel is represented by a conical structure. The app user can change design parameters ranging from the finger location to the thickness of the different layers in the sensor. The app then generates a report detailing the capacitance matrix, an integral piece of information for capacitive sensor design. The app can also show the electric field distribution in the sensor and a drop-down list can be used to select a solution corresponding to the excitation of different sensor traces.
Cypress is also using the COMSOL Server license to share their simulation apps with colleagues around the world, which allows anyone to access simulation apps using either a Windows-based client or a web browser. “We’re finding that letting our support teams have access to multiphysics simulation results is hugely helpful. We can control the parameters that the app user has access to so that we know the apps are delivering accurate results, while also letting our support engineers experiment with thousands of different design options without the need to involve an R&D engineer—or use a seat up on our COMSOL Multiphysics license.”
Test-driving Automotive Touchscreen Designs
In addition to touchscreens for consumer products, Cypress also creates touchscreen designs for use in the automotive industry. For these applications, engineers experiment with different designs in response to certain automobile requirements.
“In the automotive group, our designs are more customer driven and are often created on a case-by-case basis for a specific product or customer,” says Nathan Thomas, an R&D engineer working in the automotive group at Cypress. “Our design boxes are irregularly shaped, and we do more simulations that are customer-specific. For example, an automotive company might use touchscreens for different applications such as in the center console, in rear seat entertainment systems, or in overhead entertainment systems, all of which will need their own models.”
Instead of creating a new model for each and every instance, the automotive group is now using apps to let field engineers test new designs that would otherwise have been outside of the design box. The apps can be used to explore special requests from customers who are interested in how varying a parameter will affect end perfor-mance. “For cases such as these, we’ve been using the Application Builder to create simulation apps that our field engineers can apply directly without having to go through us to create the simulation for them. While it’s still a new technology, I can foresee simulation apps becoming the primary tool used by our field engineers.”
Powering Up
WHETHER IT BE SMARTPHONE DESIGNS, automotive applications, or other industrial processes, Cypress R&D engineers can create simulation apps that allow other support engineers to experiment with designs that would otherwise have required the expertise of an R&D engineer. Through the use of simulation, Cypress engineers are delivering more customizable designs faster than ever before.