Smart Industry is a term used for an automated and connected manufacturing facility. In Smart Industry factories produce in a more efficient manner. Factories are more flexible and customization is possible in the supply chain. Production is more sustainable with less waste and energy used. The working environment is safer and there is better man-machine cooperation in the workplace.
This article elaborate major advancements in sensors and lower power connectivity technologies which are key to the emergence of Smart connected Industry in recent times.
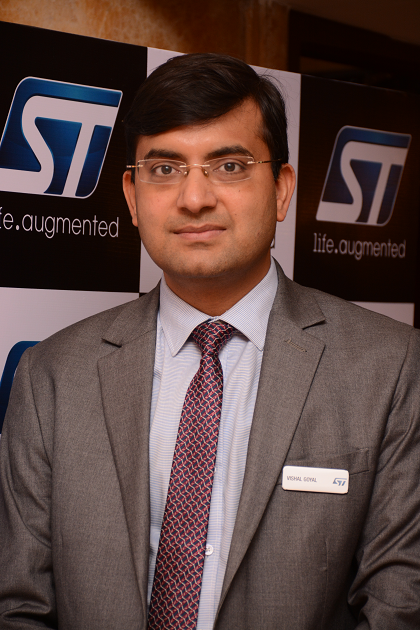
Evolution of Smart Industry
1st Industrial revolution took place in 18th century. It marks the beginning of all new machines of various types. There was mechanical equipment driven by water and steam power. The labor was responsible for entire cycle of mass production.
2nd Industrial revolution took place in 20th century. In the revolution electricity replaced water and steam as the main source of power to run the machines. It also marked the advent of the division of labor to achieve mass production. So a labor was doing a part of activity rather than whole product from beginning to end.
3rd Industrial revolution took place in 1970’s when electronics and IT get introduced to automate the process. Large mechanical machines were replaced by electronic machines. This revolution was also an important landmark for semiconductor Industry as it became the main engine of automation.
4th Industrial revolution where machines are becoming more intelligent and intuitive is witnessed today. The new machines are more efficient, safe and flexible as they can monitor their performance, usage, and failure autonomously. Big data, analytics, and decentralized decision-making techniques are used to develop robust supply chain and efficient production operation.
Machines in Smart Industries are more efficient and environmentally friendly in their production process. They are safer and offer better working experience to the workers. There is the greater two-way interaction between Human and machine. Machines are flexible in their operation, can respond to demand and can be used to produce mass customized products.
Enablers of Smart Industry
Efficiency
Smart machines have higher efficiency at all the points of their operation. They convert power from supply to the consumption in a very efficient way and when required store power very efficiently. Today Motors are much more efficient. Lighting is wirelessly controlled and used only when required.
Intelligent and aware
Machines are equipped with sensors to measure parameters such as vibration, temperature, humidity etc. The sensor information is sent to local processing unit and turned into information. Machines interact with humans around them ad provide the sensor information to them to interact with them.
Connectivity
Machines are connected to the factory, within the company and to the cloud. They provide real-time information down to lowest level and form part of a very big supply chain. The sensor information is sent to the cloud securely and is used for many analysis including breakdown prediction.
Major areas of Smart Industry
Factory Automation
Factory automation is the use of various control system to manage the production process. It allows for machines to be used sequentially with minimum human intervention. Various decision of manufacturing process can be taking by monitoring data such as humidity and temperature of the raw material and finished products, detection of a fault, automated test reports etc. Various machines can be connected in a mesh using 6LowPan subGhz RF for information sharing.
Industrial Robots
An Industrial robot is a machine with several degrees of freedom of movement. They can be programmed to do several predefined manufacturing, testing, and production tasks. They are useful in achieving high-quality manufacturing, save labor cost and even be used in the hazardous and unsuitable environment. Adoption of new generation robots, which are flexible and programmable, enable one to one product customization, according to customer’s needs and wishes. Robots are fitted with several sensors to monitor their exact position and angle. Smart robots are also wirelessly connected to send and receive inputs.
Industrial Lighting
Lighting comprises of a major portion of non-manufacturing electricity consumption of an Industrial facility. A lot of power is wasted if the lights remain ON even when it is not used. A smart lighting system can monitor and control each and every lighting using 6LowPan subGhz mesh protocol. The lights will be used only when necessary and any fault is automatically detected. Even the intensity of lights can be controlled remotely. The street light pole can also act as weather and security station.
Smart Manufacturing
Smart manufacturing is a holistic combination of various areas of manufacturing and supply chain. It encompasses automation, control, advanced robotics, motor control, sensors, connected machines etc. A smart manufacturing facility can order its raw material itself and can log on maintenance request before actual failure. It improves working condition and manages hazardous manufacturing more safely. A smart manufacturing facility also uses BIG data and artificial intelligence.
The emergence of low cost, low power sensors, and connectivity options has made smart manufacturing possible like never before.
Case Study: Machine health monitoring using automated vibration monitoring
Traditional approach
As machines are subjected to wear and tear it is necessary either to apply regular, and possibly redundant, preventative maintenance program or monitor their health periodically. A preventative maintenance program contract is given to an agency who will send its personnel periodically to monitor vibration parameters periodically. The approach is very costly as the company has to bear the cost and travel of personnel. Besides, the data monitoring is not continuous leading to high chances of failure and unpredictability.
Smart approach
Machines have permanently mounted sensor and RF connectivity modules. Sensors will monitor parameters such as vibration and temperature continuously and the information is sent to factory cloud gateway using BLE or RF subGhz. The sensors and RF connectivity modules are very low power to be even powered by battery. The data is sent to the cloud from gateway for analytics and FFT analysis.
The analysis of vibration signature of the machine enable to detect greatly in advance various type of fault or improper use such as load balance, misalignment, bearing defect, gear mesh etc.
Role of Sensors in making Industry Smart
Accelerometer
The accelerometer is used to provide the acceleration which the Industrial machines are subjected to in all three axis X, Y and Z. It also determines the tilt angle of machines or robotic arm. If the machine is stationary in a horizontal position then its X and Y axis will give 0g output whereas z-axis will give 1g output. 1g is the gravity which is experienced by every object on earth. If the machine rotates by 90deg on X axis then X and Z will give 0g and Y axis will start giving 1g. During the tilt X, Y and Z will give output which lies between 0 and 1g. The values can then be applied to trigonometry formulas to arrive at tilt angle of the machine.
Accelerometers are also used to give linear acceleration in horizontal and vertical direction. This data can be used to calculate velocity, direction and even rate of change of altitude of the machine.
Accelerometer is also used to detect the vibration which the machine is experiencing. When an accelerometer is mounted on motor it can give critical input to detect the type of fault. The frequency of fault caused by motor balance, bearing defect and gear mesh are different from one another. This information can be used to predict the maintenance requirement of motor.
Gyroscope
Gyroscope sensor detects angular velocity in three axis. So it can detect rate of change of angle in pitch, roll and yaw. The change in angle information is used to provide stability to machine and to prevent it from wobbling. The information from the gyroscope is fed to motor control drivers to control the speed of motors dynamically to provide the stability to machines or robotic arms. Gyroscope also ensures that machines or robotic arms rotate at exact angle which is expected by user controls.
Magnetic Compass
Magnetic compass as the name suggests gives the sense of direction to the machine or robotic arm. It gives data of magnetic field in three X, Y and Z which the device is subjected to. This data is then fed into algorithms in the microcontroller to give heading angle w.r.t magnetic north. This information is then used to detect geographical directions.
To get accurate direction the magnetic data should be complemented by tilt angle data from the accelerometer. The tilt data along with magnetic data will then be used to calculate accurate direction.
A magnetic compass is very sensitive to hard iron, soft iron or angle of operation. Hard iron is the presence of hard permanent ferromagnetic material in the vicinity of the sensor. It creates a permanent shift in compass reading. Soft iron is the presence of weak ferromagnetic material, circuit traces etc. It creates a variable shift in the sensor reading. So a magnetic sensor calibration algorithm is needed to filter out these anomalies. It is important for the algorithm to do a fast calibration with minimum effort by the user.
Barometer
A barometer working principle is to convert atmospheric pressure into altitude. The pressure sensor can detect earth’s atmospheric pressure. The data from Barometer helps in a machine or robotic arm navigation and achieve the desired altitude. Very good estimation of ascending and descend speeds is vital for many machines including robots. STMicroelectronics has introduced a new pressure sensor, the LPS22HD, with 200Hz of data rate to address this requirement of altitude estimation.
Humidity Sensor
The Humidity sensor can detect humidity parameter which can be used at the weather station, condensation level monitoring, air density monitoring and gas sensors measurement correction.
ST has introduced a humidity sensor HTS221 which includes a sensing element and an analog front end to provide the measurement information by the digital serial interface. The sensing element consists of a polymer dielectric planar capacitor structure able to detect relative humidity variations.
MEMS Microphone
MEMS Microphone is an audio sensor that converts sound signals into electrical signals. MEMS Microphones are increasingly preferred over conventional microphones as they offer higher SNR, small form factor, digital interface, better RF immunity and high robustness against vibration. The sensors are in machines for applications such as videography, surveillance, spying etc.
Important characteristics for sensors in Smart Industry
Machines are subjective to extreme conditions including vibration, noise, and environment. A sensor used in an industrial machine should have high shock survival capability, should capture less noise and fast enough to capture all vibration. Its performance should not vary with change in environmental parameters such as temperature and humidity. And finally, it should have high reliability and performance.
Role of Algorithms
Software libraries play an important role to convert raw sensor data into the meaningful use case. The algorithm augments the function of sensor beyond their stated features. The algorithm also combines the input from various sensors and create a context-aware output.
The three motion sensors – accelerometer, gyroscope and magnetic compass – have their own advantages and disadvantages. Sensor limitations include imperfect calibration, drift over time or temperature and random noise. Magnetometer and Accelerometer are subject to distortions and gyroscope has inherent drift. Sensor fusion library is used to calibrate their sensors with each other to create a condition which gives an accurate result in all scenarios. It not only give calibrated sensor outputs but also angles, heading angle information and quaternions.
Connectivity technologies for Smart Machines
Sub-1GHz technology is used to connect sensors network with proprietary protocol combining a real low-power consumption with long distance coverage. Cellular and Sigfox are used to collect information from the machine directly to telecom infrastructures.
The map of various technologies on scale of distance and power consumption is listed below. We will discuss lower power technologies such as BLE, RF sub-1GHz and Sigfox in a greater detail.
Bluetooth low Energy – Bluetooth Smart [BLE]
Bluetooth Smart or Bluetooth Low Energy [BLE] enables low power connectivity to machines. It is suitable for low range machines particularly the toy machines. It enables two-way communications between machines and control devices such as a smartphone, tablet, laptop and dedicated remote controller. BLE allows machines to have an incredible battery life which is not possible using traditional wireless technologies such as Wi-Fi and Classical Bluetooth.
Bluetooth Low Energy works in license free 2.4GHz ISM band. The standard is governed by Bluetooth Special Interest Group (SIG) and is support all the major smartphone brands.
There are two major partitioning available in BLE devices.
a. Network processor
A network processor is a BLE device which is running BLE protocol including controller, Host, and stack. But it needs a separate microcontroller for its functioning with the main microcontroller running BLE profiles and application. This platform is also platform independent so offers wide flexibility to the user to select best fit microcontroller or operating system. BlueNRG-MS is a network processor offered by ST and compatible with BLE 4.1. This IC can act as Master and Slave at the same time. So it is possible to have a remote controller acting as a slave to Smartphone but master of the machine.
b. System on Chip
System on Chip (SOC) is a device which is an independent chipset and includes controller, Host, stack profiles and application. BlueNRG-1 from ST is BLE 4.2 certified SOC and includes 15 GPIOs, I2C, SPI, UART, PWM, PDM and 160kB of RAM. This IC also offers advanced security and privacy features offered by BLE 4.2.
RF sub-1GHz
RF sub-1GHz as the name suggests carries the signal over sub-1GHz frequencies. Different countries have defined different frequencies which can be freely used for Industrial and scientific usage.
Below are some of the free bands available in various countries
- North America: 315, 433, 915Mhz
- Europe: 433, 868Mhz
- India : 433, 865-867Mhz
The advantage of sub-1GHz frequencies is that they are relatively quieter bands, have a longer range and consume low current. The downside is that they do not offer direct smartphone connectivity and not universally present.
Sigfox is subscription based LPWAN service based on sub-1GHz frequencies. Sigfox allows connectivity directly to telecom infrastructure and in-turn to cloud. It can give connectivity over several Km. In machines, Sigfox can be used for tracking and to send sensor data to the cloud. It is low data rate technology directly to telecom infrastructure so not expected to replace direct control connectivity options such as BLE and RF sub-1GHz direct peer to peer connection.
STMicroelectronics has recently launched RF sub-1GHz and Sigfox transceiver S2-LP. This product can communicate at 430-470 MHz and 860-940 MHz. It has output power up to +16dbm and sensitivity down to -130dbm.This extremely low current IC can be used as a peer to peer connection to establish a connection between machine and remote controller. It is also a certified Sigfox product so it can be configured to directly connect the machine to Sigfox network and then to the Cloud without gateway assuring more than 10 years battery life since its ultra-low power consumption.
Development platform
The market is evolving at such a fast pace that chancing of success depends heavily on time and cost involved. It is very important to have a development platform which is open source, affordable, flexible, production ready and scalable.
STMicroelectronics has introduced an STM32 open development environment platform which allows designers to develop products using ST microcontroller, sensors, RF and Analog products in a very flexible and affordable way. The hardware platform is complemented by software drivers, middleware libraries, and applications. It also includes associated Android and iOS code.
The user can also access many advance libraries by a simple computer-based license agreement. Once the platform is tested designer can develop his custom PCB and load the firmware developed on this platform. The user will need to sign the production license for libraries only when he wants to test on his custom board
SensorTile
SensorTile is a miniaturized tile-shaped design platform. It includes all that is needed to remotely sense and measure motion, environmental and acoustical parameters. A machine developer can straightaway focus on aerodynamics, motor control and physical design of the machine or robotic arm without worrying about connectivity and sensor integration.
The whole approach allows for preventative and proactive maintenance. The machines located in dangerous and hazardous conditions can be monitored. And company save a lot of money as it doesn’t have to pay for personnel who will no longer visit the facility.
Conclusion
Smart Industry is the need of the hour to attain higher productivity, safer working conditions, and efficiency. The advent of lower power sensor and connectivity technology has made this possible. Diverse options in sensors and connectivity are solving many complex problems which were unpractical and expensive earlier.
STMicroelectronics has more than 30 years of experience in developing products for Industrial applications. Deep application knowledge has enabled us to deliver an optimized solution. It as in-house high-quality manufacturing and owns industry-leading innovative technologies with comprehensive tools, software, and support.