The automotive industry continues to position itself at the forefront of technological developments and offers guidance for many other industries to follow. More recent developments in the automotive market have centred on electronic advancements, whether that be with much improved driver/passenger experience from improved HMI or due to safety critical developments and semi-autonomous driving features such as automatic braking and driver lane assistance, for example. Now, the focus is on the switch away from the internal combustion engine to environmentally conscious alternatives, most notably the electric vehicle (EV) and various hybrid options (HEV) and with this change comes even more challenges for electrical circuits, connectors and contacts.
Regardless of the industry, electrical contact lubricants are used to enhance the performance and reliability of electrical contacts and connectors. Originally invented in 1941 for improving the electrical performance and reliability of volume controls by Electrolube’s founder, the use of contact lubricants has spread far and wide into many different industries and has been a critical factor in the dependable performance of automotive components for decades.
Contact lubricants are specially formulated greases and oils, designed to reduce friction and wear and enhance Electric Vehicle performance of current carrying metal interfaces, such as those found in switches and connectors. As no metal interfaces are entirely even and smooth, when applied to such surfaces in thin films they fill in all surface imperfections, in turn improving contact and electrical performance as well as
prolonging the contact life by reducing hot spots, frettage and arcing.
By filling in the air gaps between the contacts, contact area, in turn preventing arcing and the related temperature rise and oxide formation. They also provide a barrier to airborne contamination and reduce the effects of friction by facilitating smooth movement. In addition, the use of contact lubricants are typically evaluated for their ‘feel’ characteristics, improving the quality of movement of a switch or in simple plastic-plastic contacts, for example.
There are 3 main ways in which contact lubricants are used in automotive applications:
To improve electrical transfer and reliability of the contact
As already discussed, contact lubricants increase the contact surface areas by filling any gaps and reducing electrical resistance. Technology has spread into more safety critical operations within vehicles and with automotive recalls due to electronic components on the rise, it is imperative that these safety critical connections are maintained correctly. In a recent report by AlixPartners, it was detailed that recalls to correct failures in electronic or electrical systems have grown 30% a year in recent years. Such failures include issues with software and software integration, however the vast majority of recalls are actually because of failures related to integrated electrical components. As an IATF 16949 approved electro-chemical solution provider, Electrolube are often asked to help prevent such issues from occurring and fully understand the impact that such failures can have on businesses, with costs coming from all areas, including the effect it has on brand reputation for the automotive manufacturer. It is therefore extremely important that all aspects of electronic systems are considered, including the connection between devices and the correct selection of a contact lubricant.
The electrical performance of a contact lubricant is usually evaluated by measuring the mV drop of the contacts/switches over a specified number of cycles. This is usually in excess of 20,000 usage cycles. The performance of various contact lubricants can vary depending on the formulation and intended end use. For example, some materials have a more stable low mV drop over a large number of cycles but compromise on their plastics compatibility, as shown in Figure 1 below. In other cases, the application may have the requirement for a particular consistency of contact lubricant, in combination with good electrical properties. A ‘stiffer’ or ‘harder’ grease may be selected in order to stay in place during the mechanical action of the switch. In such cases, the cone penetration at different temperatures or wear testing of the lubricants may assist in product selection. Conversely, a very soft grease or a contact oil may be required in applications where there is a very low contact force and in such cases, the mechanical action of the switch should be tested with a range of lubricants to determine suitability. It is therefore important to consider all electrical requirements, material compatibility and environmental influences when choosing the correct lubricant.
Traditionally, the improvement in electrical properties of switches and connectors in vehicles was focused on low voltage switches and moved on to more critical applications as the development of electronic applications progressed. With a change to Electric Vehicle, a further increased set of challenges has been posed, including more electrical connections and most notably, much higher voltages being transferred around the vehicle. With experience in industries such as medium and high voltage switchgear, electroplating and relays, Electrolube have a range of products to meet the demanding new requirements of the electric vehicle market.
To reduce the effects of external influences, reducing corrosion and wear
Acting like the central nervous system of the vehicle, the wire harness contains many connections to facilitate the communication of a multitude of devices. Due to the complexity of the electronics applications within a vehicle, the harness also accounts for a lot of weight. This has led to different materials being used, such as aluminium and in some cases, differing metals could be used within the same harness. Whilst reducing weight, there are also other challenges with using aluminium, including the formation of hard oxide layers and electrochemical corrosion in the presence of moisture and differing metals. Contact lubricants can be used to protect freshly mated contacts being exposed to the environmental conditions but this is only part of the problem. During the lifetime of these contacts, corrosion caused by fretting is common and the use of a contact lubricant to prevent the exposure of any base materials on contacts or aluminium parts can greatly reduce failure rates of contacts and connectors.
Environmental influences can include temperature changes, humidity exposure and corrosive atmospheres. Changes in temperature can affect the consistency of the contact lubricant, for example, a lubricant may have a cone penetration value of 320 at 25˚C but when exposed to temperatures of -40˚C or lower, this value may significantly reduce, resulting in a much harder consistency of grease. Humid environments are also common and most contact lubricants will withstand high humidity for prolonged periods. When high humidity is combined with corrosive environments, differences between products can be realised. Electrolube have designed a series of tests to illustrate these differences and provide further assistance with correct product selection. These tests include wetting humidity followed by salt mist tests, chlorine resistance tests and consideration of different contact materials.
The combined humidity and salt mist testing subjected the lubricants to 90% humidity at 35˚C for 3 weeks, followed by 1 week at 35˚C in the salt mist chamber. The protection of copper and steel substrates was visually evaluated after this test. Typically, the synthetic lubricants, such as Electrolube CTG provided the best protection in this environment. In addition to this test, gold and silver contacts protected with various lubricants were also subjected to the salt mist environment. Results further strengthened previous findings, highlighting that some mineral based lubricants in particular are not suitable for protecting these materials in harsh environments. Finally, as an extreme test, an oxidative environment containing chlorine was created and maintained at 35˚C for 2 months and results again showed that Electrolube CTG provided exceptional protection, closely followed by Electrolube CG53A and CG60.
To improve the quality, feel and insertion force/operation of connectors and switches.
Contact lubricants are also widely used in many applications to improve the ‘feel’ of a switch, thus giving the impression of high quality. This is also true for many applications within the interior of vehicles, ensuring that metal-metal, plastic-metal and plastic-plastic contacts alike have a good connection between parts, thus reducing noise and movement when subjected to vibrations caused by the normal operation of the vehicle. With a move towards quieter vehicles, improvements in tyre technology and the future with Electric Vehicle, the vehicle interior is a much quieter place to be and as such, the quality of these contacts and overall noise dampening is essential to ensure a high quality driving experience is achieved.
Products such as Electrolube’s CG60 and SPG have been used for such automotive applications for many years and are suitable for futureproofing the interior of vehicles, ensuring the upmost of comfort in the driving experience. In some cases, a fluorinated lubricant, such as Electrolube’s EGF, may be required to offer greater performance in these areas and particularly in the case of reducing the insertion forces when mating connectors. This again leads us to a discussion about the wire harness and with the increase in number of electronic components and connectors as we move towards Electric Vehicle, the need for lubricants such as Electrolube’s CG60, CTG or EGF for improving manufacture and in-use protection is also greatly increased. In fact, in a study by Research and Markets it is reported that based on component, the connection of electronics within vehicles via wire harnesses is projected to witness the fastest growth up to 2025 due to the development of advanced technologies in the automotive field, including driver assistance systems and safety features.
The automotive industry is in a period of constant change and evolution. By switching to HEV’s and EV’s, a new set of challenges for electrical connectors, switches and devices are being put forward and will also continue to evolve for years to come. Developments in battery technology and user interfaces, alternative fuel sources, and the ever expanding autonomous driving market, will all add to these challenges. By addressing the seemingly small task of ensuring high quality, reliable and protected connections, contact lubricants will assist in meeting these new demands. The Electric Vehicle powertrain is on average two and a half times more expensive than conventional powertrains (AlixPartners), leading to cost being another barrier for growth in this market. This cost will naturally come down over time with economies of scale and improvements in technologies. This, combined with reduced overall costs resulting from the maintenance of high quality levels and reduced vehicle recalls due to connector failures, is why manufacturers need to have the choice of contact lubricants high on their development agendas now and for many years to come.
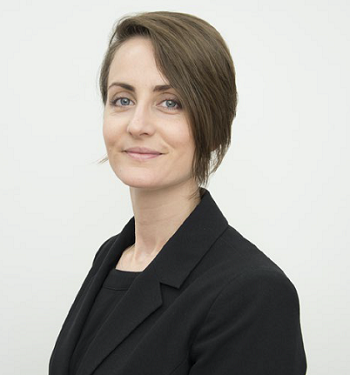