A brushless DC motor consists of a rotor in form of a permanent magnet and stator in form of polyphase armature windings. It differs from conventional DC motor in such that it doesn’t contains brushes and the commutation is done using electrically, using an electronic drive to feed the stator windings.
Basically a BLDC motor can be constructed in two ways- by placing the rotor outside the core and the windings in the core and another by placing the windings outside the core. In the former arrangement, the rotor magnets act as an insulator and reduce the rate of heat dissipation from the motor and operates at low current. It is typically used in fans. In the latter arrangement, the motor dissipates more heat, thus causing an increase in its torque. It is used in hard disk drives.
4 Pole 2 Phase Motor Operation
The brushless DC motors is driven by an electronic drive which switches the supply voltage between the stator windings as the rotor turns. The rotor position is monitored by the transducer (optical or magnetic) which supplies information to the electronic controller and based on this position, the stator winding to be energized is determined. This electronic drive consists of transistors (2 for each phase) which are operated via a microprocessor.
The magnetic field generated by the permanent magnets interacts with the field induced by the current in the stator windings, creating a mechanical torque. The electronic switching circuit or the drive switches the supply current to the stator so as to maintain a constant angle 0 to 90 degrees between the interacting fields. Hall Sensors are mostly mounted on the stator or on the rotor. When the rotor passes through the hall sensor, based on the North or South Pole, it generates a high or low signal. Based on the combination of these signals, the winding to be energized is defined. In order to keep the motor running, the magnetic field produced by the windings should shift position, as the rotor moves to catch up with the stator field.
In a 4 pole, 2 phase brushless dc motor, a single hall sensor is used, which is embedded on the stator. As the rotor rotates, the hall sensor senses the position and develops a high or low signal, depending on the pole of the magnet (North or South). The hall sensor is connected via a resistor to the transistors. When a high voltage signal occurs at the output of the sensor, the transistor connected to coil A starts conducting, providing the path for the current to flow and thus energizing coil A. The capacitor starts charging to the full supply voltage. When the hall sensor detects a change in polarity of the rotor, it develops a low voltage signal at its output and since the transistor 1 doesn’t get any supply, it is in cutoff condition. The voltage developed around the capacitor is Vcc, which is the supply voltage to the 2nd transistor and coil B is now energized, as current passes through it.
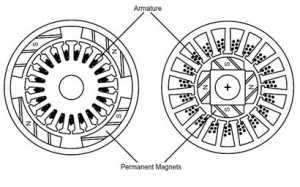
BLDC motors have fixed permanent magnets, which rotate and a fixed armature, eliminating the problems of connecting current to the moving armature. And possibly more poles on the rotor than the stator or reluctance motors. The latter may be without permanent magnets, just poles that are induced on the rotor then pulled into arrangement by timed stator windings. An electronic controller replaces the brush/commutator assembly of the brushed DC motor, which continually switches the phase to the windings to keep the motor turning. The controller performs comparative timed power distribution by using a solid-state circuit instead of the brush/commutator system.
Seven Advantages of Brushless DC Motors
- Better speed versus torque characteristics
- High dynamic response
- High efficiency
- Long operating life due to a lack of electrical and friction losses
- Noiseless operation
- Higher speed ranges
Applications:
The cost of the Brushless DC Motor has declined since its presentation, because of progressions in materials and design. This decrease in cost, coupled with the numerous focal points it has over the Brush DC Motor, makes the Brushless DC Motor a popular component in numerous distinctive applications. Applications that use the BLDC Motor include, yet are not constrained to:
- Consumer electronics
- Transport
- Heating and ventilation
- Industrial engineering
- Model engineering
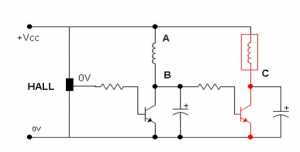
Principle of Working
The principles for the working of a BLDC motors are the same as for a brushed DC motor, i.e., the internal shaft position feedback. In case of a brushed DC motor, feedback is implemented using a mechanical commutator and brushes. Within BLDC motor, it is achieved using multiple feedback sensors. In BLDC motors we mostly use Hall-effect sensor, whenever rotor magnetic poles pass near the hall sensor, they generate a HIGH or LOW level signal, which can be used to determine the position of the shaft. If the direction of the magnetic field is reversed, the voltage developed will reverse too.
Controlling a BLDC Motor
Control unit is implemented by microelectronic has several high-tech choices. This may be implemented using a micro-controller, a dedicated micro-controller, a hard-wired microelectronic unit, a PLC or similar other unit.
Analog controller are still using, but they cannot process feedback messages and control accordingly. With this type of control circuits it is possible to implements high performance control algorithms, such as vector control, field oriented control, high speed control all of which are related to electromagnetic state of the motor. Furthermore outer loop control for various dynamics requirements such as sliding motor controls, adaptive control, predictive control…etc are also implemented conventionally.
Beside all these, we find high performance PIC (Power Integrated Circuit), ASIC (Application Specific Integrated Circuits) …etc. that can greatly simplify the construction of the control and the power electronic unit both. For example, today we have complete PWM (Pulse Width Modulation) regulator in a single IC that can be replace the entire control unit in some systems. Compound driver IC can provide the complete solution of driving all six power switches in a three phase converter. There are numerous similar integrated circuits with more and more adding day by day. At the end of the day, system assembly will possibly involve only a piece of control software with all hardware coming the right shape and form.
PWM (Pulse Width Modulation) wave can be used to control the speed of the motor. Here the average voltage given or the average current flowing through the motor will change depending on the ON and OFF time of the pulses controlling the speed of the motor i.e. The duty cycle of the wave controls its speed. On changing the duty cycle (ON time), we can change the speed. By interchanging output ports, it will effectively change direction of the motor.
Speed Control
Speed control of BLDC motor is essential for making the motor work at desired rate. Speed of a brushless dc motor can be controlled by controlling the input dc voltage. The higher the voltage, more is the speed. When motor works in normal mode or runs below rated speed, input voltage of armature is changed through PWM model. When motor is operated above rated speed, the flux is weakened by means of advancing the exiting current.
The speed control can be closed loop or open loop speed control.
Open Loop Speed Control – It involves simply controlling the dc voltage applied to motor terminals by chopping the dc voltage. However this results in some form of current limiting.
Closed Loop Speed control – It involves controlling the input supply voltage through the speed feedback from the motor. Thus the supply voltage is controlled depending on the error signal.
The closed loop speed control consists of three basic components.
- A PWM circuit to generate the required pwm pulses. It can be either a microcontroller or a timer IC.
- A sensing device to sense the actual motor speed. It can be a Hall Effect sensor, an infrared sensor or an optical encoder.
- A motor drive to control the motor operation.
This technique of changing the supply voltage based on the error signal can be either through pid controlling technique or using fuzzy logic.
Application to Speed Control of Brushless DC Motor
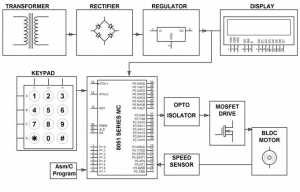
The motor operation is controlled using anoptocoupler and MOSFET arrangement, where input DC power is controlled through pwm technique from microcontroller. As the motor rotates, the infrared led present at its shaft gets illuminated with white light due to presence of white spot on its shaft and reflects the infrared light. The photodiode receives this infrared light and undergoes change in its resistance, thus causing a change in supply voltage to the connected transistor and a pulse is given to the microcontroller to generate the number of rotations per minute. This speed is displayed on the LCD.
The required speed is entered in the keypad interfaced to the Microcontroller. The difference between the sensed speed and the desired speed is the error signal and the microcontroller generates the pwm signal as per the error signal, based on the fuzzy logic to give the dc power input to the motor.
Thus using closed loop control, the speed of the brushless dc motor can be controlled and it can be made to rotate at any desired speed.