Courtesy: Comsol
Picture this: A battery pack is connected to a charger and is left to recharge. The first minute passes without incident, with electricity flowing into the pack as expected. Suddenly, one battery cell experiences a short circuit and rapidly heats up, which in turn sparks a chain reaction as other cells in the pack follow suit. By the time 20 minutes have passed, the entire battery pack has been completely ruined. To explore this potentially dangerous scenario, we modelled a battery pack as it endures this rapid change.
The Risks of Batteries Going Wrong
Batteries can experience thermal runaway when they are pushed beyond their normal operating range, subjected to damage, or suffering from a short circuit, like in our dramatic example above. During this process, a battery cell heats up uncontrollably and triggers adjacent cells to follow suit. When excessive heat generation is not counteracted by sufficient dissipation, the whole pack exhibits thermal runaway. This can quickly damage the entire battery pack beyond use. In worst case scenarios, the extreme temperatures can even start fires, with potentially dire consequences.
To get insight into how this type of failure could develop and progress in prospective designs, battery designers can turn to modeling and simulation (M&S) to test their designs without damaging any materials — or themselves, for that matter — in the process. M&S makes it possible to look inside the battery pack in a way that is impossible in a lab setting and multiphysics simulation, specifically, ensures that the models reflect the real-world context in which the battery pack will eventually live.
Building a Battery Pack Model in COMSOL Multiphysics
Let’s take a look at a simple pack of 20 cylindrical batteries in a 5s4p configuration. In a 5s4p configuration, 4 sets of battery cells are connected in parallel, and each set contains 5 serially connected individual battery cells. For this model example, we included two plastic holder frames to keep the batteries in their locations and fix the cell-to-cell distances. The model also has parallel connectors welded to the serial connectors, midway between the battery cylinders, and a thin plastic wrapping that encloses the whole pack. This wrapping forms a compartment of quiescent air surrounding the battery cylinders.

The model uses the following materials from the material library in the COMSOL Multiphysics software:
- Acrylic plastic (for the plastic holders)
- Steel AISI 4340 (for the connectors and battery terminals)
- Air (for the air in the compartment)
Next, let’s trigger thermal runaway in the pack! To initiate our propagation, we assume that one cell endures a short circuit early in the charging process.
Modeling Thermal Runaway
In our simulation, as soon as the short circuit is triggered (at the 1-minute mark) the maximum measured temperature within our battery pack instantaneously increases by more than 300°C. However, the average temperature only jumps moderately as just one battery cell experiences this dramatic increase in temperature. We see an incubation period during which nearby cells are warmed by our problem cell until another cell is triggered to heat up instantly.
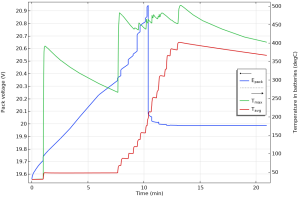
The threshold temperature for the remaining cells to be triggered into experiencing a thermal event is 80°C and, with the overall heat growing in the battery pack, the intervals between successive cell runaways become shorter. To simulate the loss of electrolyte and the resulting increase of internal cell resistances, the internal ohmic resistance of a battery cell is set to increase about two orders of magnitude when a thermal event is triggered.
At the 10-minute mark, the maximum charging voltage limit has been reached and the charger is turned off. Unfortunately, this has come too late to prevent further damage, and the thermal runaway continues to propagate throughout the rest of the pack. After just a few more minutes, we have lost all 20 of our battery cells. The thermal processes have run their course by the 20-minute mark, but the average temperature of our battery pack remains at more than 350°C. Had this been a real battery pack, the modelled scenario would likely have resulted in a fire, or even an explosion.
Prevent Problems Before They Arise
Batteries that have been kept too hot, operated in an unsafe way, or damaged, can experience thermal runaway events. When one part of the system begins to overheat, things can rapidly devolve. By modeling these events, users can virtually test their designs and verify, for example, the effectiveness of battery management systems as well as the temperature regulation of the system in potential deployment locations. It is through this approach that thermal runaway events can be better understood and, hopefully, avoided altogether.