Overview
Industrial systems have radically changed the way they communicate in the past two decades and we have seen a shift from fieldbus-based systems to Ethernet-based communications systems. A study by MarketsandMarkets projects that the overall market for Industrial Ethernet to rise from US$9.2 billion in 2020 to US$13.7 billion by 2026, at 7.3% CAGR during the forecast period.
There are several reasons behind the rapid uptake of the Industrial Ethernet, beginning with the shortcomings of fieldbus-based systems. While the latter offers simple control functionality and shows periodic improvements, limitations such as speed, remain unaddressed. As manufacturers strive towards an Industry 4.0 strategy, the need for speed is high as modern applications, in particular robotics, demand complex and precise control. As a result, Ethernet-based implementations become an alternative solution.
Ethernet offers a number of benefits, beginning with its capacity to accommodate most industrial use cases, including the most challenging Industry 4.0 applications. Plus, it is a well-established global protocol that is also cost-effective, and most importantly, versatile in its usability for diverse applications. For example, it allows easy and economical integration of older fieldbus applications into the Ethernet backbone. Another key benefit is the availability of engineers who are well-versed in how the technology works. However, the Ethernet in IT systems is non-deterministic – the network’s ability to guarantee that an event will occur in a specified and predictable period of time. This is a significant limitation as Industry 4.0 demands a strong alignment between industrial operations and IT systems and therefore, communications systems need to comply with the same standards.
Several new standards – Ethernet TSN, EtherNet/IP, PROFINET, EtherCAT – emerged as manufacturers and companies tried to address the deterministic requirement by developing an Ethernet-based standard that would work for industrial systems. For the most part, these new standards adapted the Ethernet, which had its foundation in IT, to suit the real-time demands of industrial operations. They have succeeded in creating niche acceptance specific to a geography or technology. On the other hand, Ethernet for Control Automation Technology (EtherCAT) is slightly different from these Industrial Ethernet implementations as it retains the standard Ethernet physical layer while building it up with a new deterministic protocol.
Differentiators of the EtherCAT network
The EtherCAT protocol has a host controller, the sole device with the power to create the EtherCAT frame, which is always of the same length. A unique addressable area of the frame is assigned to each device node within the network. As the frame moves from one node to another along the network, each node receives the control data and leaves its corresponding response data in the allocated area as it passes through. There is no delay except what is caused by hardware propagation. This results in a maximum effective data rate that nearly matches the line speed (100 Mbit/s).
This kind of speed is not achievable in other implementations as the various steps involved – the frame check, CRC check, and passing through the stack – can consume hundreds of microseconds. In contrast, EtherCAT is built to complete it all in a mere 125µs, making it highly responsive, rendering the control application to be more safe and efficient. Another advantage is the reduced complexity and cost of the system as EtherCAT’s device node has a relatively simpler design and only needs a stack code (SSC) operated by a simple microcontroller.
Fixing the drawbacks of EtherCAT implementation
Manufacturers, in particular those who use motors, aim to implement control algorithms at a cycle time of 125 µs, equivalent to 8,000 cycles per second. EtherCAT implementation may become complicated due to the difficulties designers face to meet these cycle time requirements. Although it seems easily achievable, it has been demonstrated difficulties in practice and entails considerable writing and optimization of software. This can also be costly – for example, a ready-made DIN-rail EtherCAT controller that accompanies a motor controller can cost hundreds of dollars. A workaround that uses a custom design is recommended as it can be nearly ten times less than the original cost.
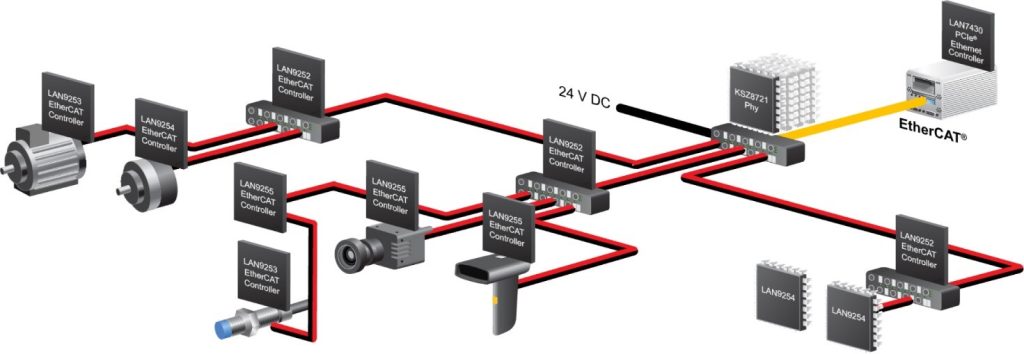
Microchip entered the EtherCAT market a decade ago and launched its first EtherCAT device controller (ESC), the LAN9252, in 2015. Following its market success, we have had the opportunity to understand the typical challenges associated with EtherCAT implementation and realized that users want a more convenient solution to meet cycle time requirements as well as value-added features in the implementation that would help them better understand EtherCAT’s operations.
Based on these feedbacks, we developed our next generation of ESC solutions. Brought to market in September 2020, the LAN9253 and LAN9254 devices include three port ESCs that comprise a dual integrated Ethernet PHYs with a full-duplex 100BASE-TX transceiver and 100Mbps operation.
Redesigning ESC solutions to simplify EtherCAT implementations and operations
Traditionally, EtherCAT implementations employ an ESC, a microcontroller and an EEPROM that is responsible for the hosting configuration for the ESC. In keeping with the original ambition of helping designers, our team fine-tuned the new ESCs to meet cycle time requirements with minimal software optimization. In addition, we made it easier to implement EtherCAT nodes by reducing the design time and BoM. Microchip devised a technique to match the EEPROM’s performance wherein the ESC uses a function call to retrieve instructions directly from the host microcontroller, thus eliminating the need for an EEPROM to be physically included.
Multi-axis controllers are used in applications like robotics and designing them can be quite a challenge – nearly half a dozen controller circuits are required to operate a multi-axis robot arm and each circuit needs a dedicated crystal for timing. We revamped the design by adding a feature in the new ICs to reduce the quantity of crystals used for timing. This was achieved through a process of accurately replicating the clocking system and jitter attenuator for all the circuits with one crystal rather than six, which further reduced system cost.
Previously, the EtherCAT protocol did not provide diagnostics feature in the physical layer. Therefore, users could not anticipate problems but could only learn about degradation of the cable and other faults once errors such as CRC errors began to occur. As a result, Microchip focused on the ability to predict faults before they became a problem as this is an important principle of Industry 4.0. We built in the monitoring feature that made it possible for users to continuously oversee the condition of cables and predict a problem ahead of its occurrence.
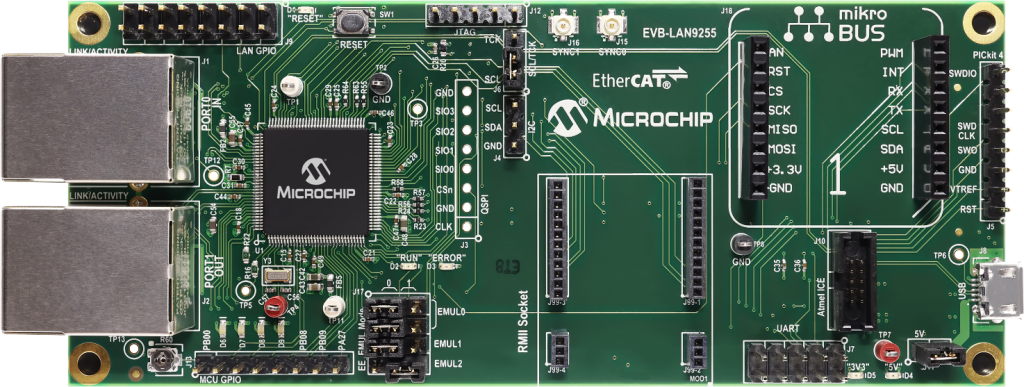
The LAN9253 resides in a QFN package – the pin-out is a close replica of the LAN9252’s package. Users can therefore gain maximum benefits of the design improvements with minimal redesign. 16 new I/O pins are included in the LAN9254 that help the ESC function like a simple controller without the inclusion of a microcontroller. By using our knowledge of certain fixed parameters such as the area of the frame used by the device node and the propagation delay, we have designed the ESC such that bits can be mapped to offsets in the frame and 32 I/O lines – this mapping ensures that field equipment are directly linked to the EtherCAT network.
Another key insight from our customer feedback exercise was the need for a controller that would serve as a one-stop ESC solution. Our latest launch, the LAN9255, attempts just that. It includes a Cortex-M4F microcontroller that can attain the speed needed to accommodate the EtherCAT requirements. At the same time, it doubles as the control system’s application processor which includes a floating-point unit that can support more complex algorithms, such as in motor control. Additions such as the Ethernet sockets with code support for SNMP version 3 boost the flexibility of the network when the operational technology needs to be linked to the IT infrastructure.
Extending the power of EtherCAT
Microchip’s LAN9253 and LAN9254 offer an innovative approach to make the transition to EtherCAT a more efficient experience by easing up the processes and time involved in implementation and maintenance of EtherCAT nodes. These also offer a cost-effective and efficient solution by removing supporting components in the design while adding valuable features to improve software optimization and network diagnostics. The new LAN9255 IC extends the impact by eliminating the role of an external host controller and offers developers a unique package that encompasses an EtherCAT node and field control solution. Furthermore, the Microchip MPLAB X Harmony Framework can be effectively employed to reach the market faster as software for both communications and control can be conveniently written and optimized in the same user environment.
Authored Article by: Ian Saturley, Microchip Technology