The blogs show how to overcome the problem of jerky motion caused by conventional stepper motor controllers in pan-tilt-zoom (PTZ) surveillance cameras. Unfortunately, stepper motors also have the undesirable reputation of being amongst the loudest – for example, if you’ve ever watched a 3D Printer in action, you possibly noticed how the motors audibly whine. For stepper motors to be effective in surveillance camera applications, this audible noise must be reduced dramatically, otherwise, an intruder would quickly be alerted to a camera’s presence, allowing them to take evasive action. The noise produced by a stepper motor may even interfere with the audio feed accompanying the camera’s video signal. This blog discusses the two main contributors to stepper motor noise – vibration and current ripple – and conventional approaches to overcoming them. It then considers additional improvements made by Analog Device’s Trinamic team, enabling the much smoother and quieter stepper motor performance required for effective surveillance camera operation.
Overcoming problem No. 1 – Vibration
By design, a stepper motor moves through a fixed number of mechanical steps – typically 200 full steps per revolution – corresponding to 1.8 degrees per step. They have traditionally used “full-stepping” control where stator phase coils are energized to generate magnetic fields that push the rotor to the next full step (represented by the alternating-colored notches at the rotor’s edge in Figure 1). However, when transitioning between steps, the rotor is not subject to any form of control, and this causes jerking which transfers into the motor housing, resulting in mechanical vibrations that produce audible noise.
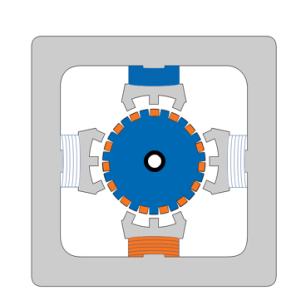
Microstepping – a form of controlled movement between full steps – is the first stage in solving the problem of noise caused by vibrations. This involves having the motor driver generate a precise control current to move the rotor to an intermediate position between each full step. The most common approach is to use 16 microsteps per full step i.e., a 1/16 microstep. While this reduces vibrations, it does not eliminate them completely. Seeking to further improve on this, Analog Devices’ Trinamic team developed a much higher resolution motor driver with 1/256 microsteps. This results in exceptionally smooth movement between full steps, dramatically lowering the level of vibration, and hence the level of noise produced. Figure 2 shows the incremental benefits of increasing resolution. With full-step control, the change in drive current is rapid, leading to oscillations around the target value. As the number of microsteps increases, oscillations begin to decrease, and the current waveform moves closer to the ideal sinusoidal shape required for smooth motion.
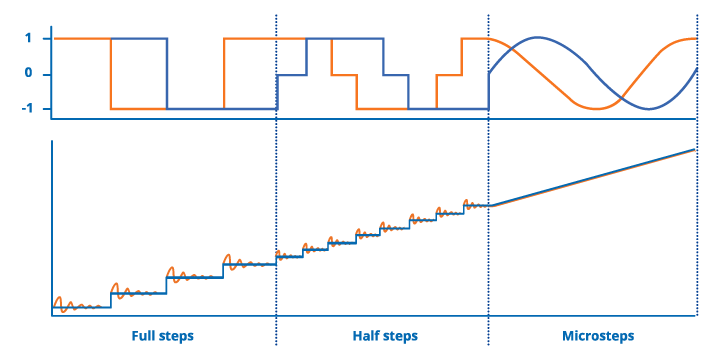
Overcoming problem No. 2 – Current Ripple
Building on the benefits of microstepping, the second stage is endeavoring to make the motor control current as sinusoidal as possible. The conventional current-mode approach allows the motor driver to monitor and adjust the current, and to change MOSFET switching frequencies. Unfortunately, constantly changing the switching is necessary because stepper motors nearly always produce a few millivolts of measurement noise, but this has the unwanted side-effect of producing audible noise.
Analog Devices’ Trinamic team solved this problem by developing a voltage (instead of current) control approach called StealthChop, which performs pulse width modulation (PWM) of the control voltage. Using a fixed frequency prevents the audible noise caused by changing the switching frequency. Figure 3 compares the motor coil voltages using current control versus Stealthchop. With StealthChop there is no visible frequency jitter in the motor control voltage.
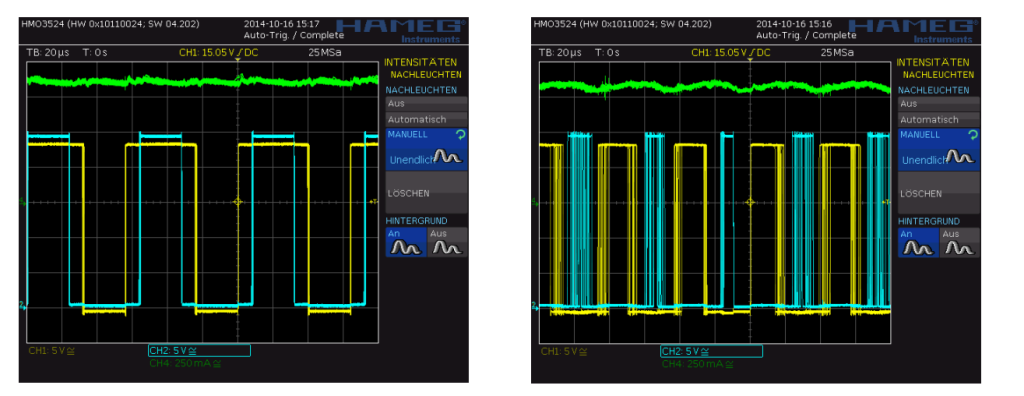
Furthermore, apart from reducing audible noise, StealthChop produces a sine wave with a much smoother profile, providing the extra advantage of further reducing vibrations. For an effective PTZ surveillance camera, using StealthChop with 1/256 microstepping represents the optimal approach for low noise and vibrations.